Exploring the Essentials Understanding Common Nail Factory Operations
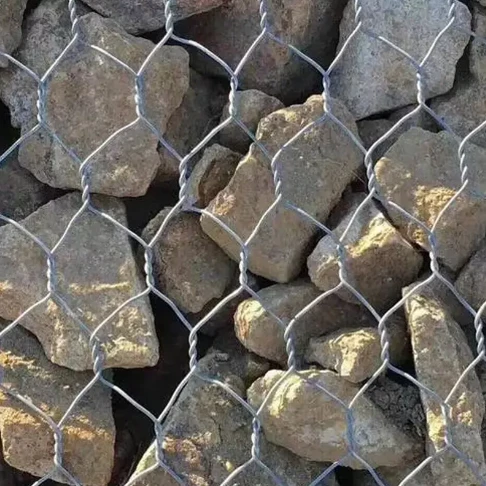
In the industrial realm of construction supplies, the common nail has emerged as an elemental component, vital for a plethora of building and household projects. Understanding the intricacies of a common nail factory provides invaluable insights into production methodologies, industry standards, and quality parameters crucial for anyone involved in construction or manufacturing.
A common nail factory employs a combination of precision engineering and cutting-edge technology to produce nails that conform to strict industrial standards. Each factory follows a meticulously crafted production process, beginning with the selection of raw materials. Typically, high-quality carbon steel wire, known for its durability and resilience, serves as the foundational material. The factory ensures that this material source is consistent and sustainable, underscoring the industry's commitment to ecological responsibility.
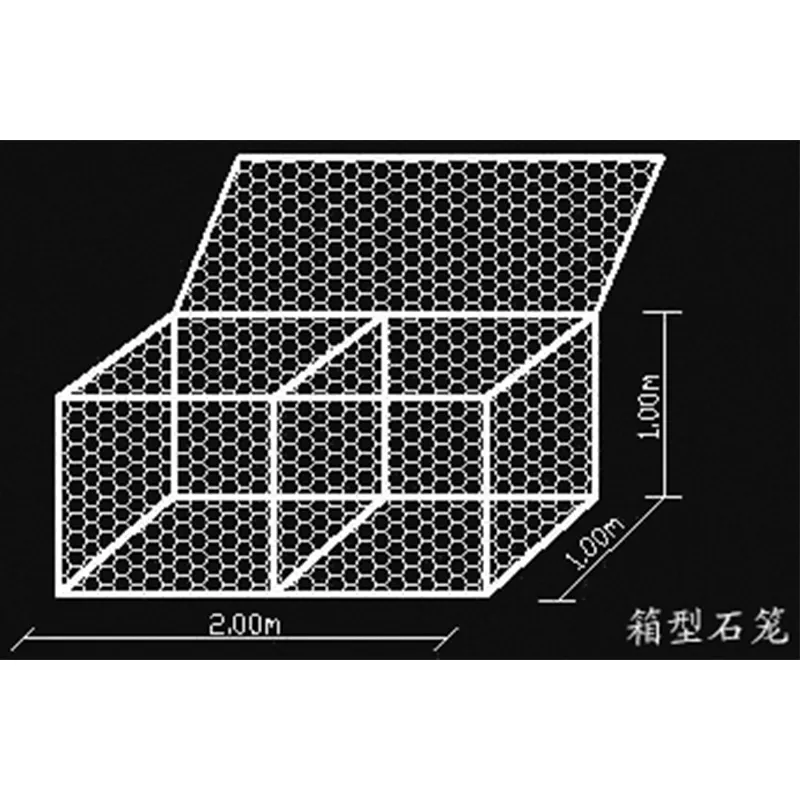
Once the steel wire passes quality checks, it undergoes a forming process where it is fed into machines that cut it to the desired length. These machines are equipped with advanced die sets to create the nail heads. A key to a factory's success is its ability to maintain precision in this phase, as it directly influences the balance and security of the nail's hold when used in construction.
The next stage involves heat treatment, a crucial process contributing to the nail's strength and corrosion resistance. Within the controlled environment of a heat treatment chamber, nails are subjected to high temperatures, enhancing their tensile strength and durability. Many factories employ a specialized coating process thereafter, adding galvanization or other anti-corrosive layers. This step is particularly significant in extending the lifespan of nails, making them suitable for both indoor and outdoor applications.
common nail factory
An aspect that showcases a factory’s expertise is its ability to innovate in nail design. While the fundamental concept of a nail — a pointed metal piece used to hold materials together — may seem elementary, variations such as ring shank, smooth shank, and spiral nails are developed to meet specific needs. Each type requires distinct manufacturing tweaks and quality controls, demonstrating the factory’s adaptability and specialization capabilities.
Authoritativeness in the nail manufacturing industry is built upon adherence to stringent regulations and quality standards. Reputable factories comply with ASTM codes (American Society for Testing and Materials) and ISO (International Organization for Standardization) certifications. These endorsements signify that the factory meets or exceeds international quality benchmarks, bolstering its credibility and ensuring customer trust.
Trustworthiness is also anchored in transparency and customer engagement. Leading factories often offer virtual tours, presentations, and detailed reports of their production processes to stakeholders, fostering an environment of open communication. Client testimonials and long-standing partnerships further embellish a factory’s reputation, providing tangible evidence of reliability and excellence.
In choosing a common nail factory, one must consider not just the cost but the amalgamation of all these factors — technical expertise, creative innovation, adherence to quality standards, and an unwavering commitment to customer satisfaction. These pillars form the backbone of a manufacturing entity capable of producing nails that not only meet the immediate requirements of building tasks but also offer longevity and peace of mind.
Ultimately, a comprehensive understanding of common nail factory operations serves as a testament to the industry’s intricate nature and its significant role in supporting global construction and manufacturing endeavors. This knowledge is invaluable for stakeholders aiming to make informed decisions, ensuring that every nail counts, quite literally, in the grand architectural tapestries we seek to create.