Galvanized mesh has become a huge game-changer in the industrial and construction sectors, merging robustness with the versatility that modern projects demand. In my extensive experience of over two decades as a material specialist, I have consistently advocated for the use of galvanized mesh, given its near-immunity to the adverse effects of rust and corrosion. Such traits inherently extend the lifespan of any structure in which it is incorporated — a feature often overlooked until considerable repair costs arise.
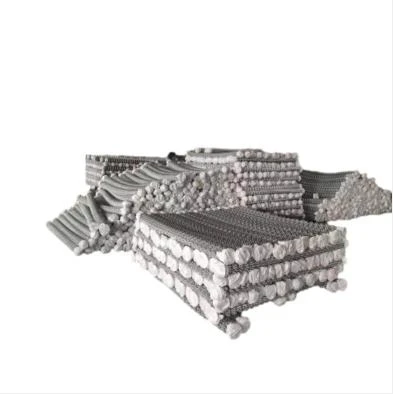
The expertise required to truly appreciate galvanized mesh comes from understanding its composition and processes. This mesh is usually crafted from mild steel and then coated with a layer of zinc. The protective layer of zinc shields the underlying steel from moisture and environmental corrosives, ensuring it remains intact even in damp or outdoor conditions. This resistance not only contributes to added longevity but also maintains the integrity of the mesh under various stressors.
With galvanized mesh being available in different designs like welded or woven, its application spans much more than just fences. In construction, it's used in reinforcing concrete to bolster its tension abilities, providing strength and durability to a range of architectural feats. My firsthand experiences on numerous construction sites reveal that reinforced concrete using galvanized mesh often exceeds standard lifespan expectations.
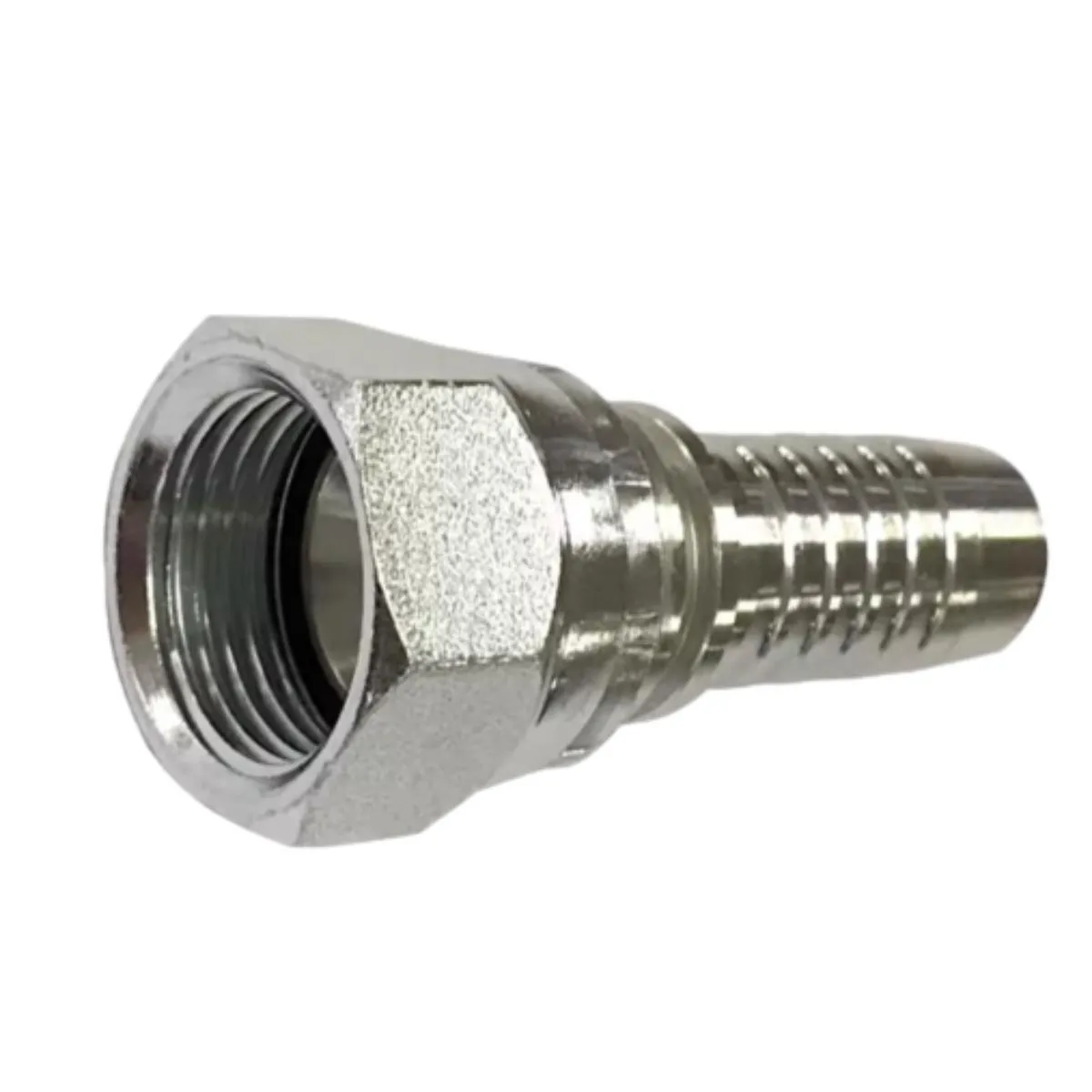
The authoritativeness of galvanized mesh is clear when considering its certification and widespread usage. Many quality assurance standards like ASTM and ISO delineate guidelines for its production and use, ensuring it meets stringent safety and durability criteria. Such endorsements from recognized bodies underscore its reliability and authenticity as a product that upholds structural integrity while respecting industry standards.
Trustworthiness is another pillar that stands tall for galvanized mesh. Unlike other materials, its performance is consistent and predictable, traits that architects and engineers have come to rely on implicitly. I recall a project where an alternative material choice led to an unplanned overhaul due to rust compromising the structure, significantly hiking the costs. Using galvanized mesh as a preventive measure can save not only costs but also time and energy, eliminating unforeseen project delays.
galvanized mesh
Its applications are not limited to construction alone. Various industries, including agriculture and fabrication, utilize galvanized mesh too. In agriculture, for example, it forms the backbone of durable enclosures and chicken coops that must withstand harsh weather conditions. Fabricators incorporate it into products where aesthetic appeal meets practical durability, such as decorative partitions and room dividers. Versatility, an inherent trait of galvanized mesh, ensures it maintains a significant role in diverse environments.
While alternative materials may present cost-benefit scenarios initially, they cannot match the lifespan and structural benefits of galvanized mesh. This becomes evident when analyzing long-term total cost ownership—durability and reduced maintenance of galvanized mesh often result in overall savings, even if the initial outlay might be slightly higher. In line with sustainability trends, it's imperative to mention that galvanized mesh is also environmentally friendly; the zinc used in its protective coating can be recycled, contributing to greener building practices.
In industrial applications, specially designed galvanized meshes find use in filtration systems and sieves due to their resilience. These critical components demand consistency and reliability, qualities that galvanized mesh articles deliver without fail. Its resistance to chemical exposure in industrial environments further secures its position as indispensable in settings that require robust, dependable materials capable of enduring ongoing exposure to caustic materials.
Galvanized mesh, thus, represents more than just a product choice — it mirrors a commitment to embracing efficiency and reliability. Clients and project managers can work with confidence, knowing remarkable results are achievable without the looming shadow of subsequent failure and replacement.
In conclusion, galvanized mesh is not merely a component but rather an investment into renewable cycles of quality, consistency, and sustainability. Every product landscape should thoroughly examine the capacities galvanized mesh unlocks –– an assurance of structural fortitude backed by expertise, authority, and an uncompromising reputation for trustworthiness.