Welding mesh has become an essential material across various industries, prized for its versatility, durability, and cost-effectiveness. Understanding the factors that influence the price of welding mesh can significantly impact budget planning and ensure procurement efficiency.
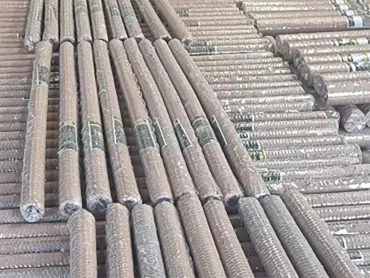
Firstly, the price of welding mesh largely depends on the material used. Stainless steel mesh tends to be more expensive compared to galvanized steel due to its superior corrosion resistance and durability. Yet, in applications where long-term performance and minimal maintenance are crucial, like in coastal structures, the investment in stainless steel becomes invaluable. Professionals who rely on the longevity of materials often argue that the initial higher expenditure on stainless steel welding mesh pays off through reduced replacement frequency.
Another critical factor affecting welding mesh price is the mesh size and gauge. The gauge refers to the thickness of the wire used; higher gauges mean thinner wire, which translates to lower manufacturing costs. Consequently, lighter mesh options are typically more cost-effective but may sacrifice some structural integrity. Understanding the balance between cost and the strength required for specific applications is pivotal. For heavy-duty construction projects, experts suggest opting for lower gauge welding mesh despite the higher cost, as it provides the necessary reinforcement.
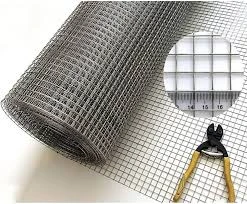
Production processes also influence pricing. Automated production lines enable manufacturers to produce mesh in large volumes at reduced costs due to economies of scale. Investing in suppliers known for their advanced production techniques can lead to cost savings. It's beneficial to engage with manufacturers who offer transparency in their production processes, often indicating a commitment to quality and reliability.
welding mesh price
Geographical location plays a role in welding mesh pricing as well. Transportation costs can significantly influence the final price. Procuring mesh from local suppliers can minimize these expenses, making it crucial to consider regional suppliers who have acclimatized to local market demands and logistical challenges. Industry veterans often recommend building strong relationships with local distributors for better pricing and reliability in delivery.
The demand within different sectors also affects market prices. As construction and infrastructure projects boom, the demand for welding mesh rises, subsequently pushing prices up. In such scenarios, volume purchasing agreements can be beneficial. Procuring in bulk can leverage price reductions and secure stock availability, which is particularly advantageous during peak industry cycles.
Lastly, certification and compliance with industry standards can affect welding mesh pricing. Products that meet international standards like ISO or ASTM might be priced higher due to the assurance of quality they provide. Industries with stringent safety and performance requirements should prioritize certified welding mesh, which, although pricier, diminishes risks of compliance issues or structural failures.
In conclusion, while the welding mesh price can fluctuate based on various factors such as material choice, production processes, and market demand, making informed decisions can yield long-term cost benefits and project successes. Collaborating with reputable suppliers who demonstrate expertise and a track record of trustworthiness is prudent. Fostering these relationships ensures not just competitive pricing, but also a consistent supply of quality products tailored to industry needs. By prioritizing expert guidance and aligning purchase strategies with project goals, professionals can navigate the complexities of welding mesh pricing with confidence and achieve sustainable outcomes in their endeavors.